Scaling Impact
ADM is paving the way with good business practices, progressive solutions and mindful actions that make a positive impact.
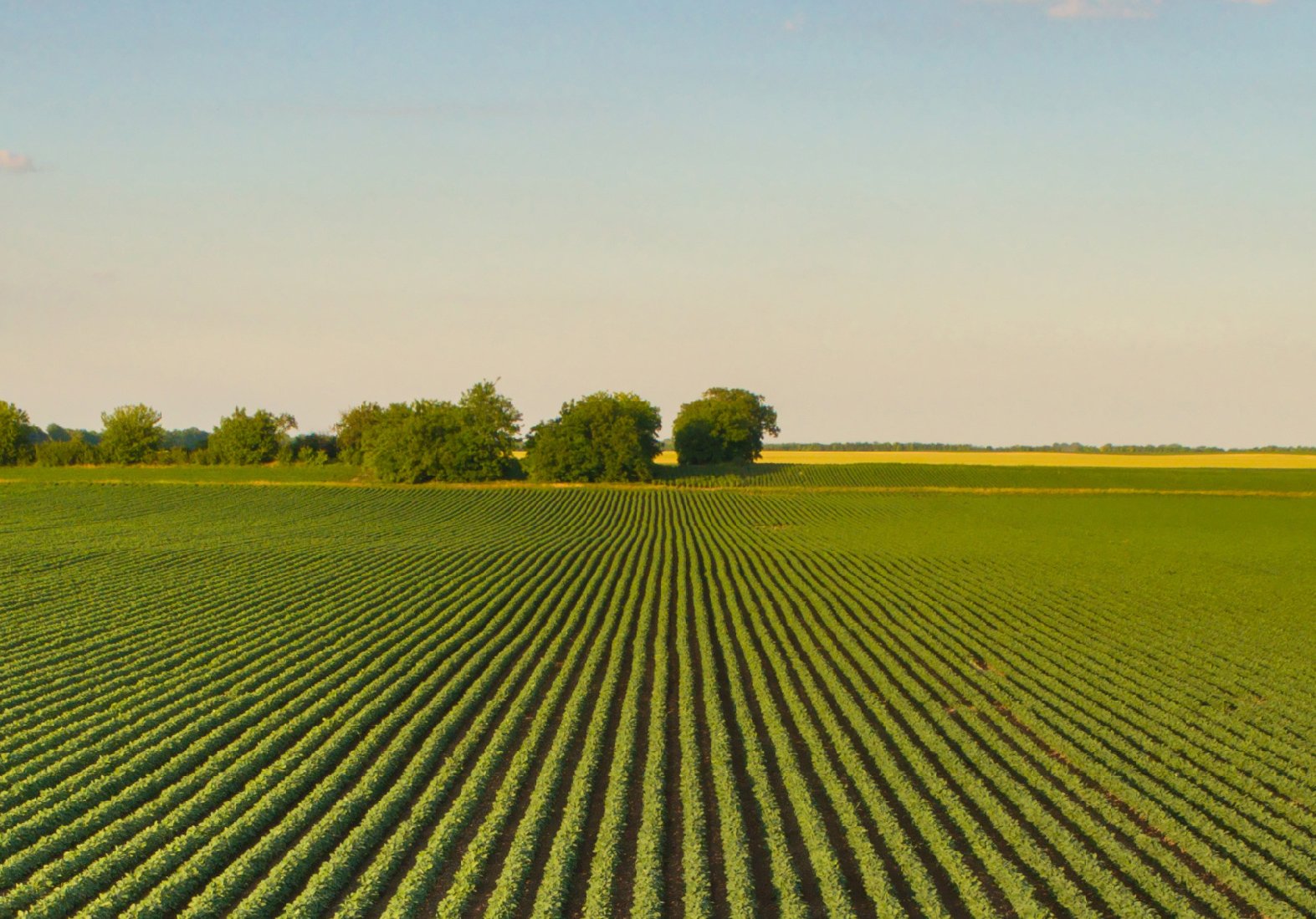
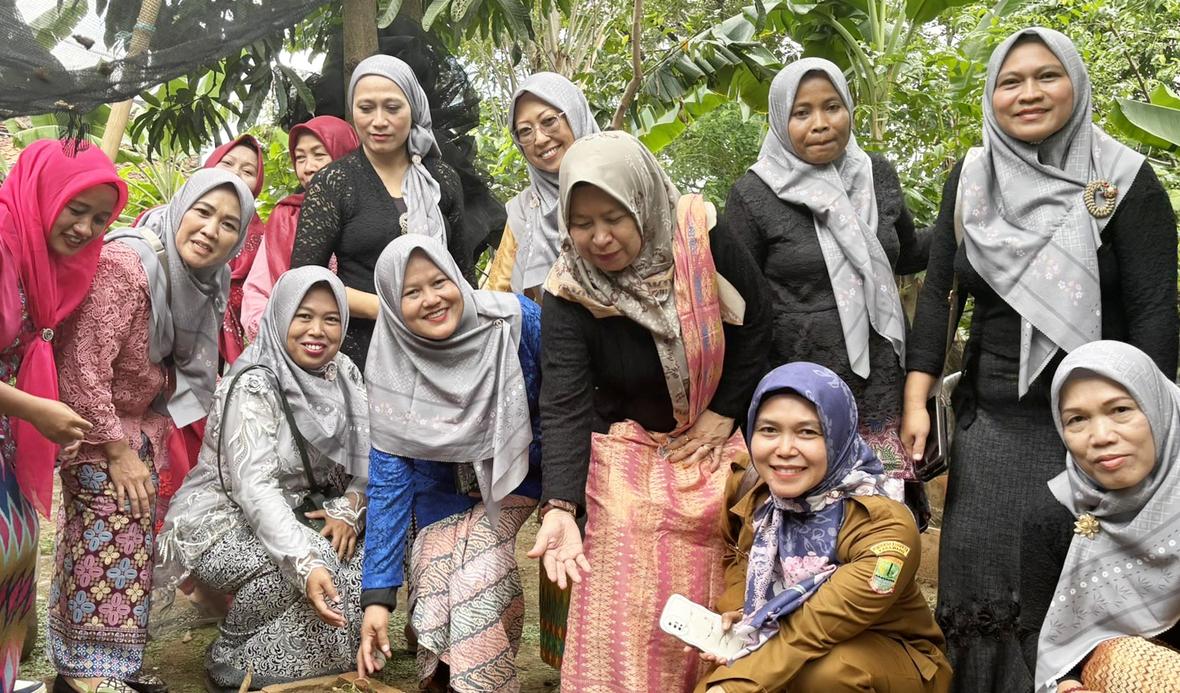
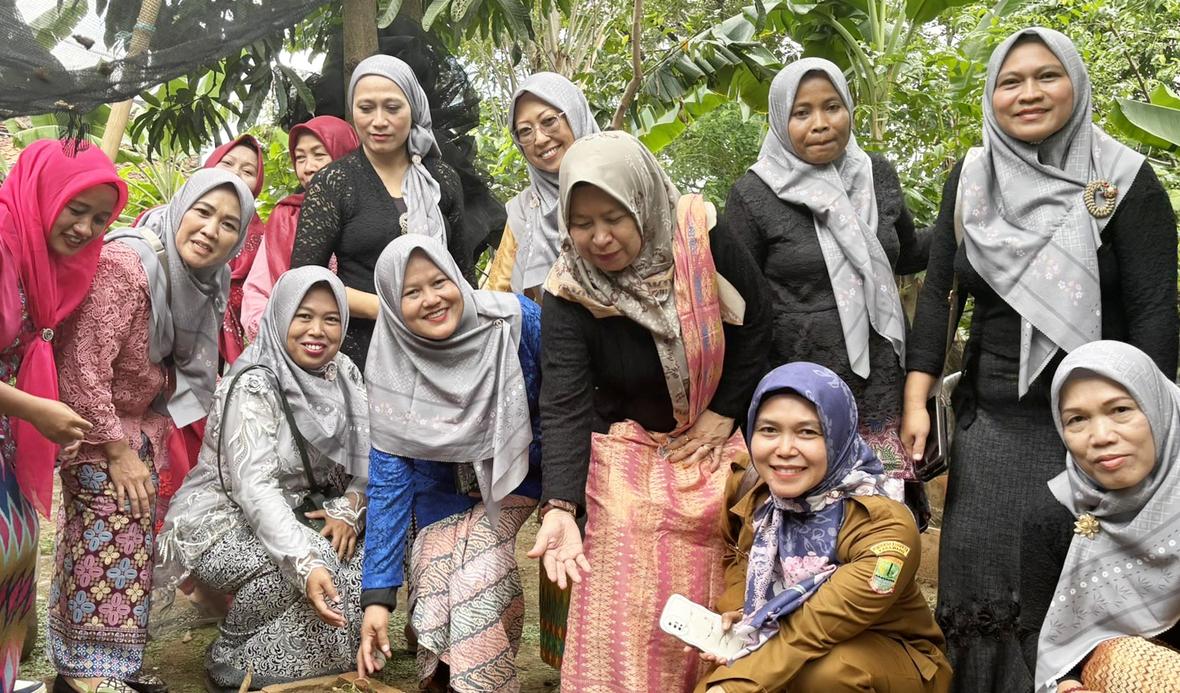
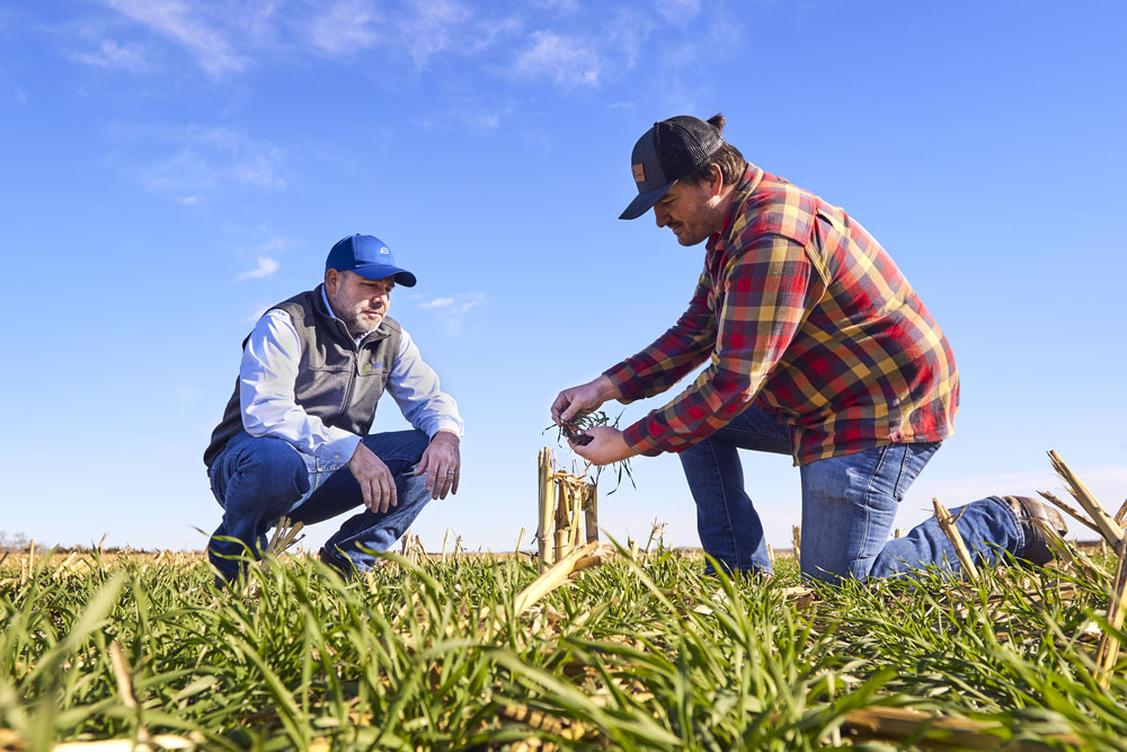
Sustainability at ADM
Program Areas
Biodiversity
We work to protect habitats in our supply chains through our commitments to no-deforestation and no-conversion.
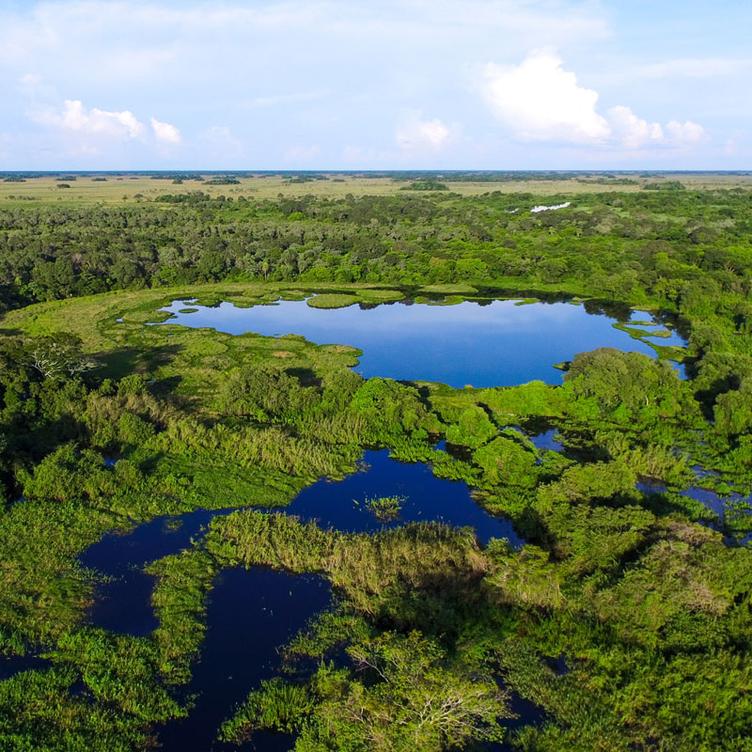
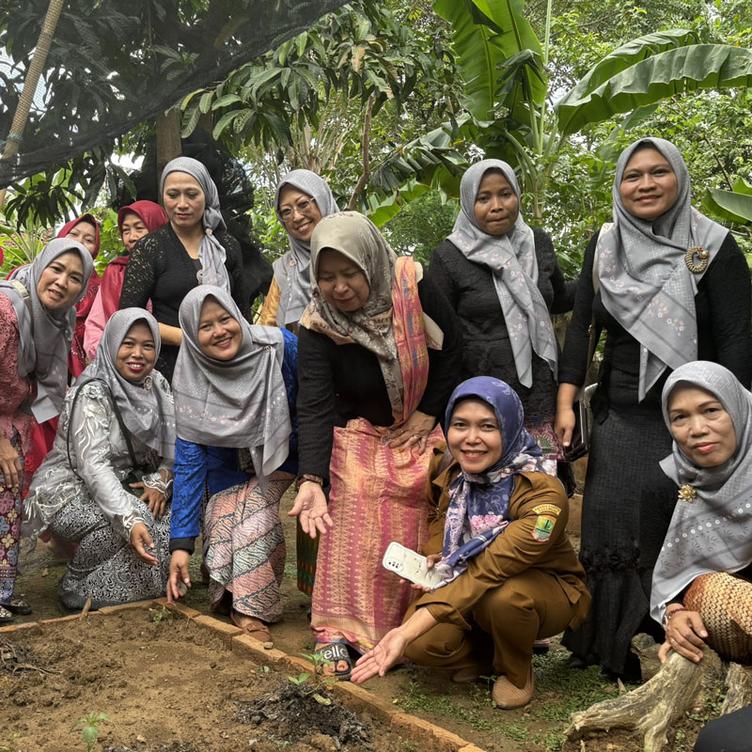
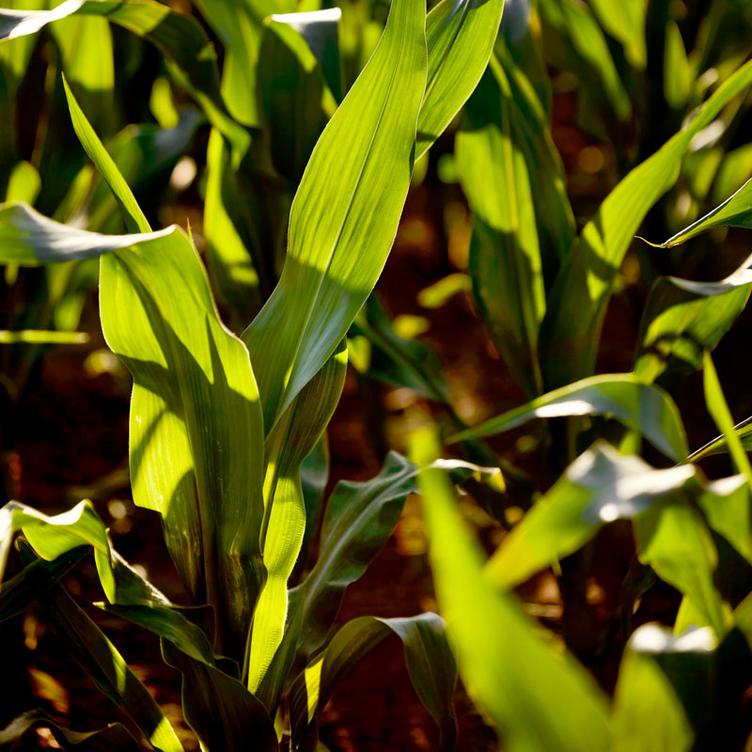
Climate
We focus on implementing projects that manage our risks by reducing our carbon footprint in our operations and spanning our supply chains.
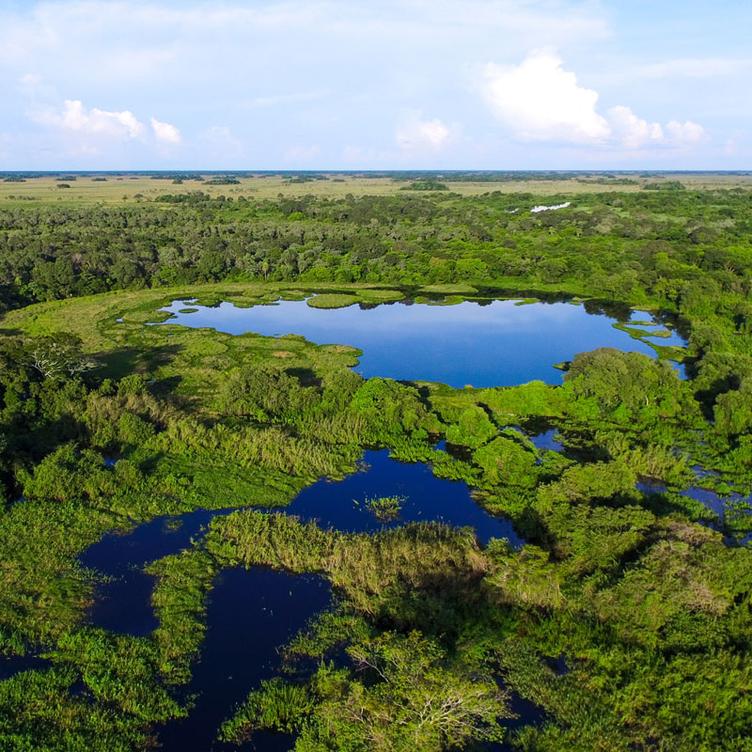
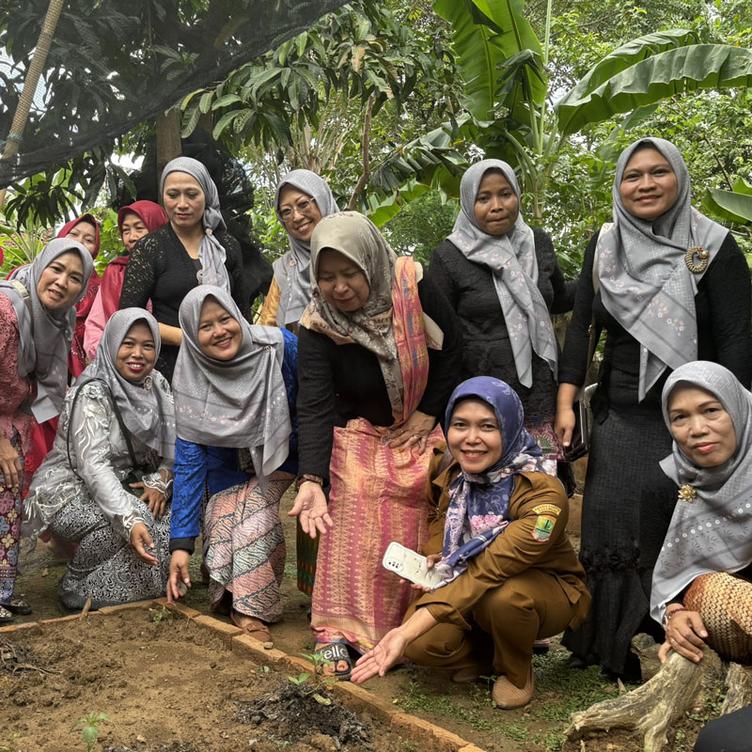
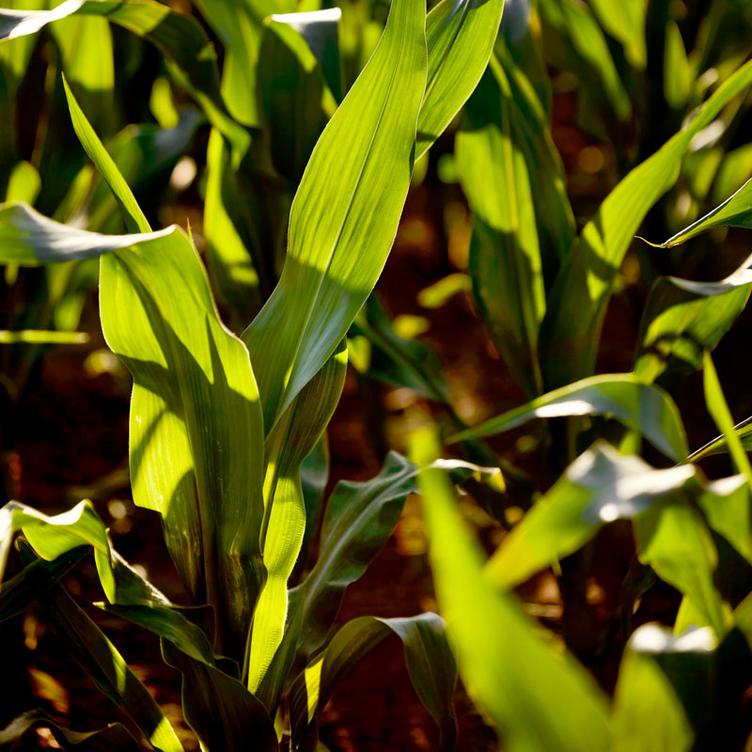
Human Rights
Our dedication to upholding human rights is central to our purpose and foundational to our work spanning the value chains in which we operate.
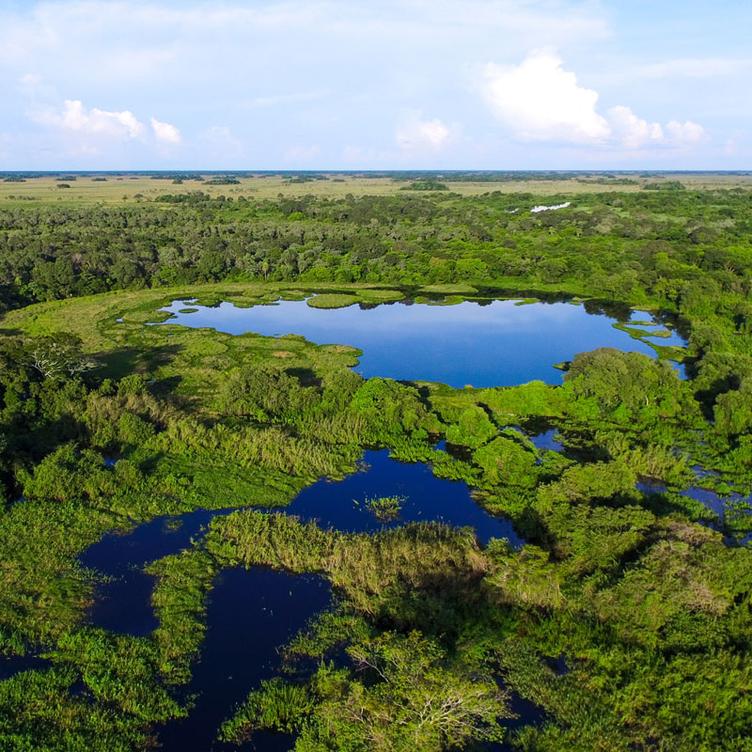
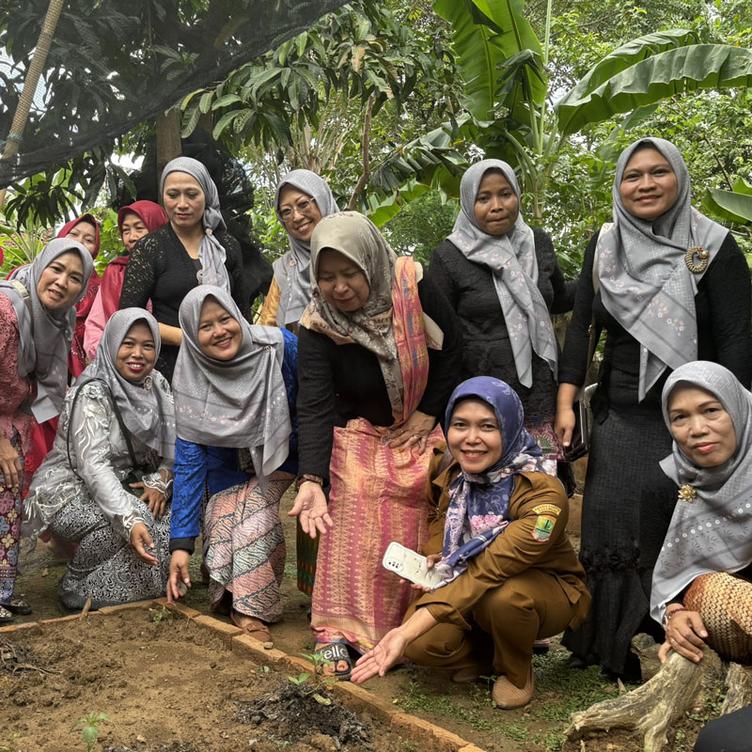
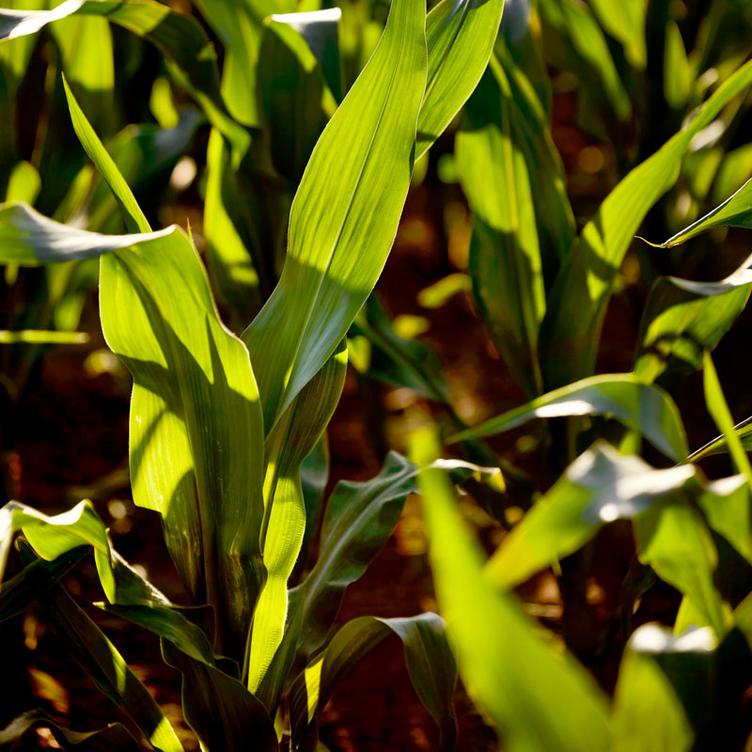
Regenerative Agriculture
We engage with growers around the world on implementing sustainable and regenerative agricultural practices.
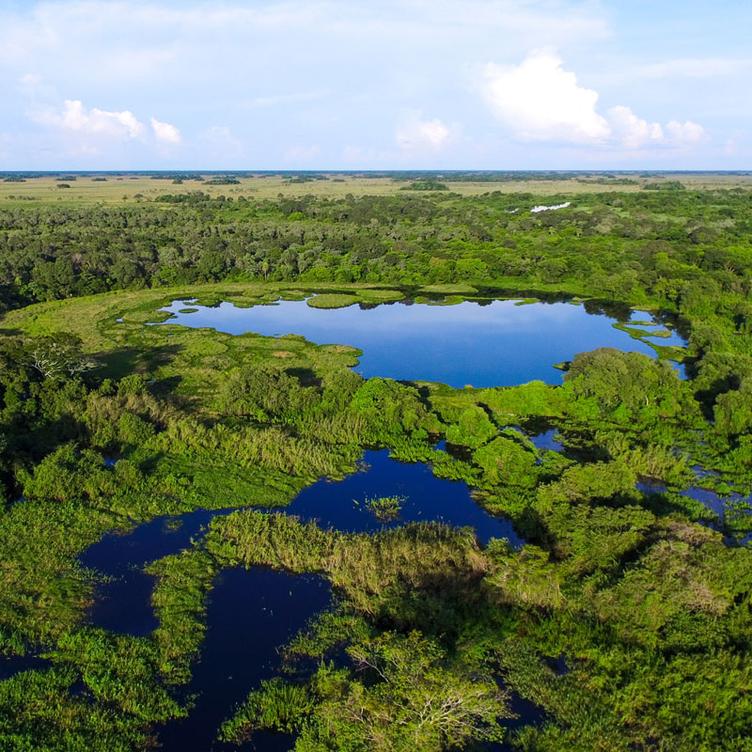
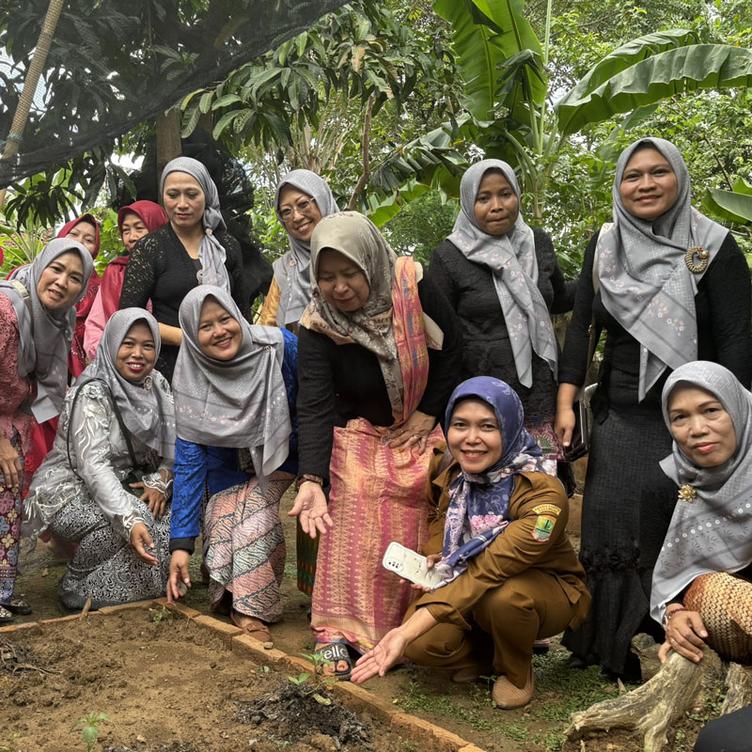
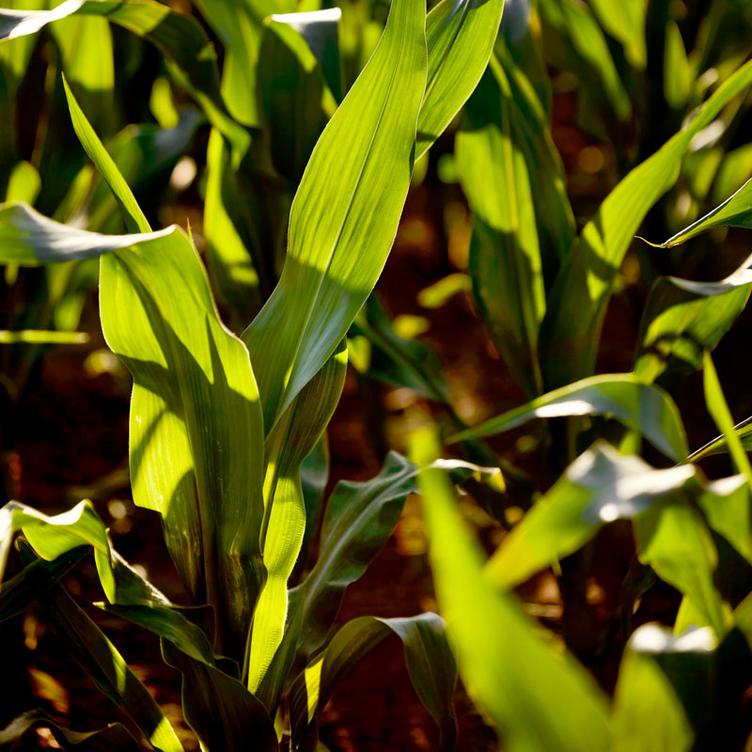
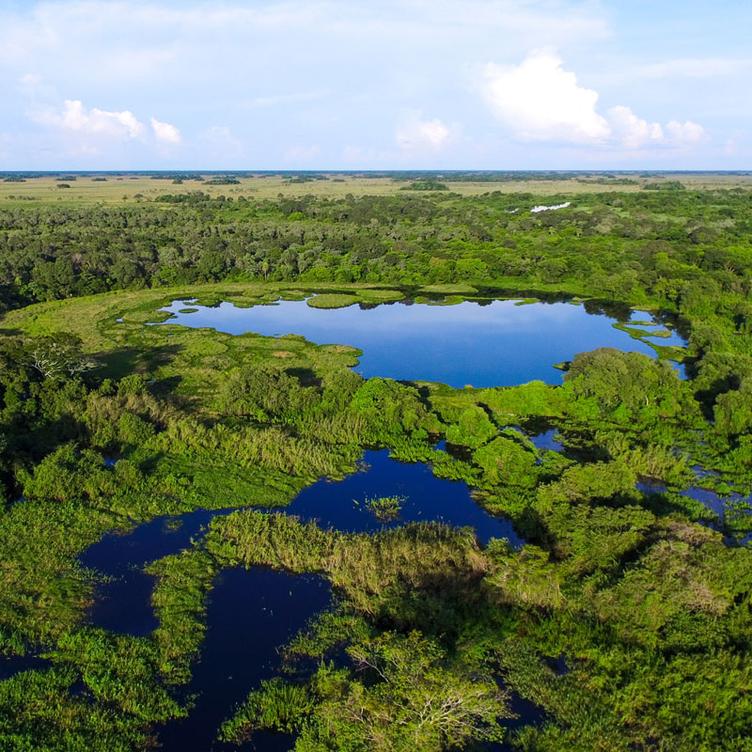
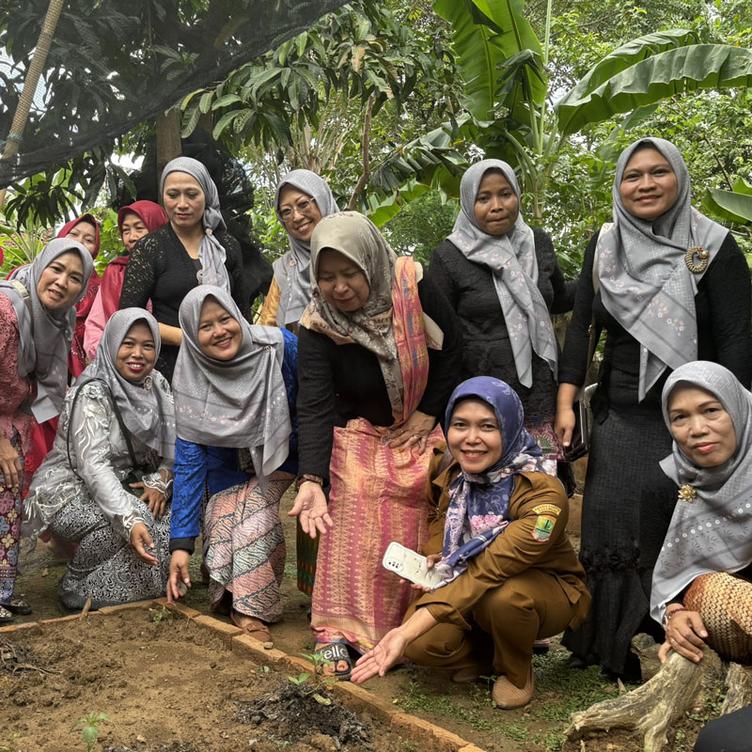
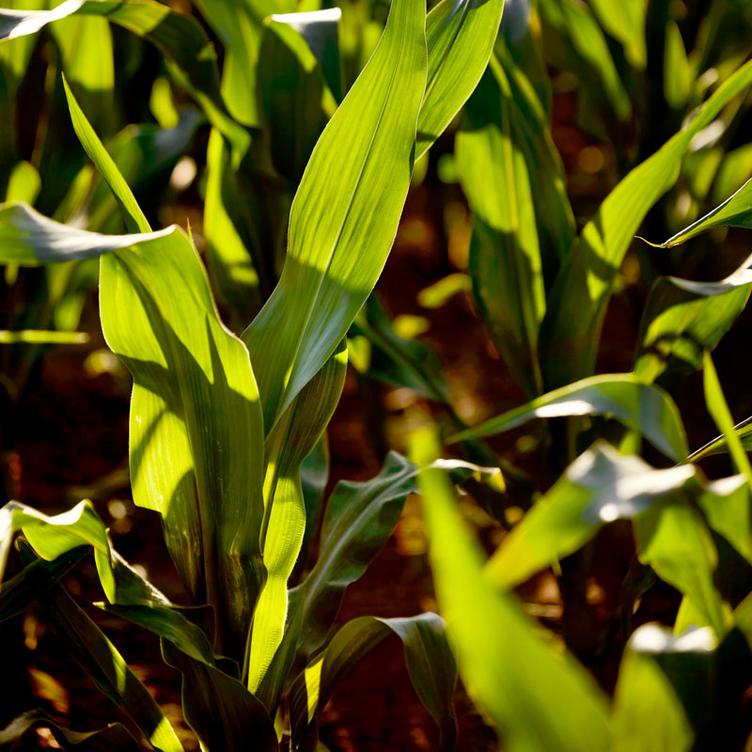
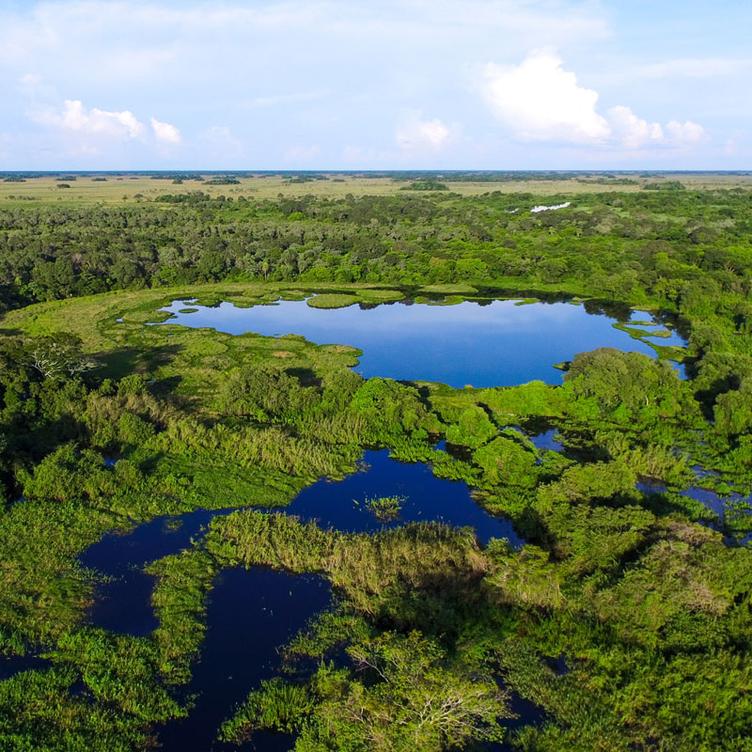
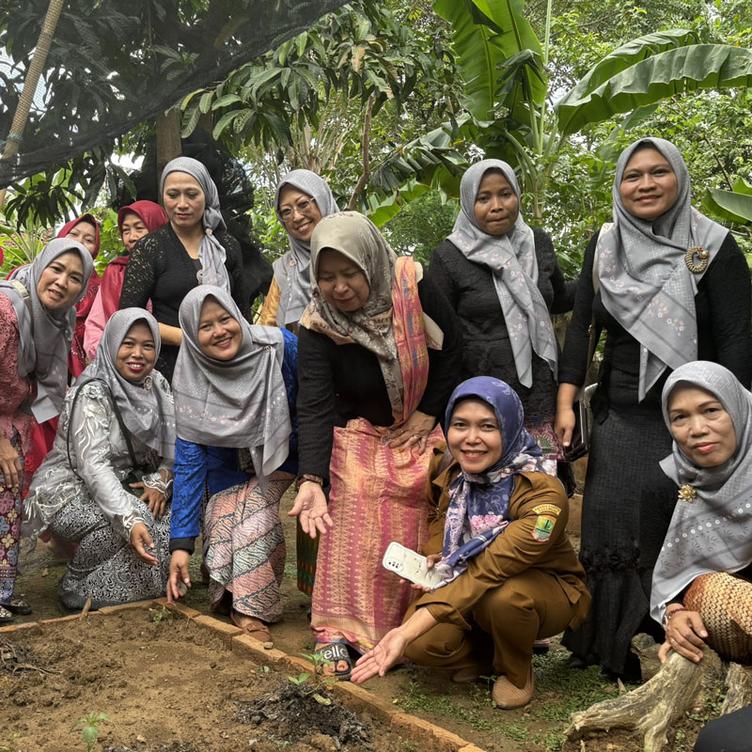
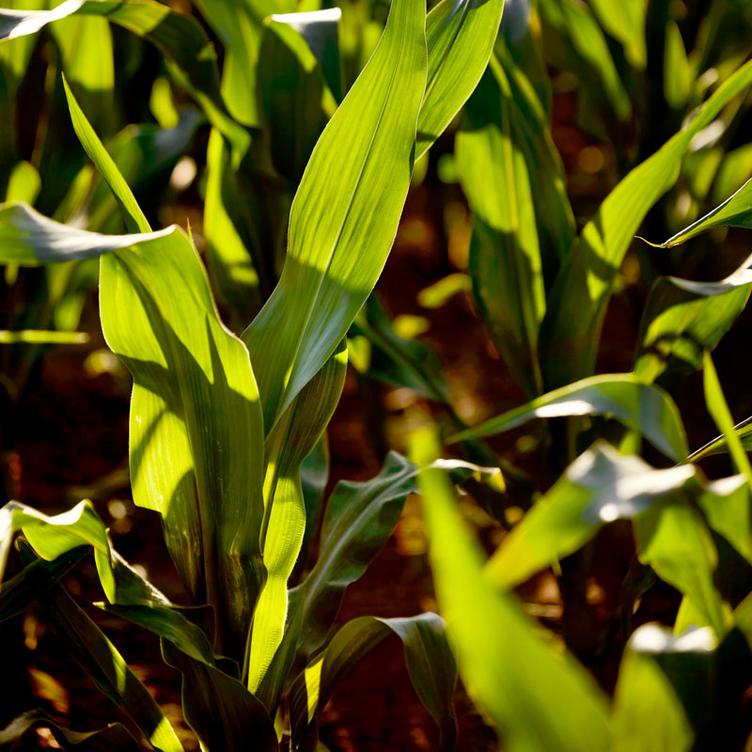
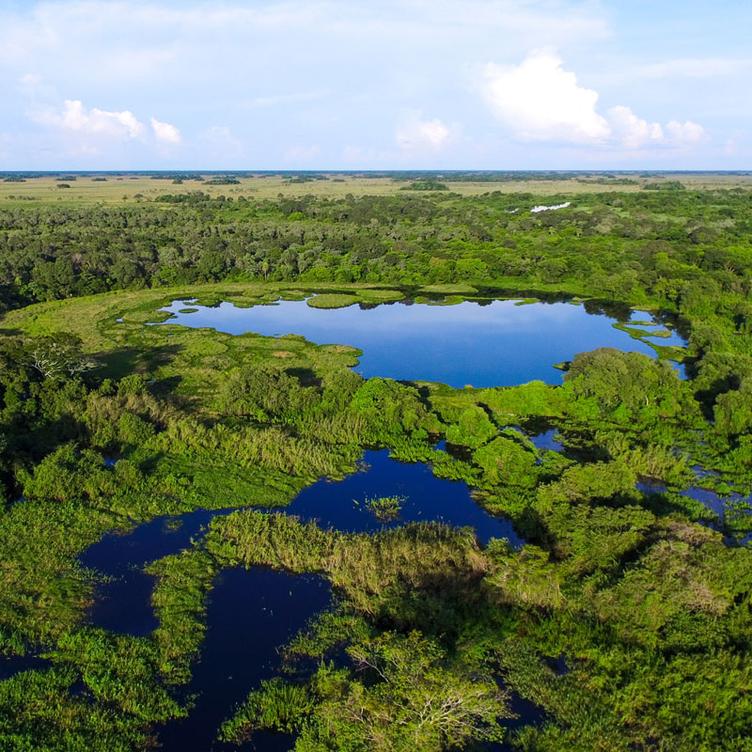
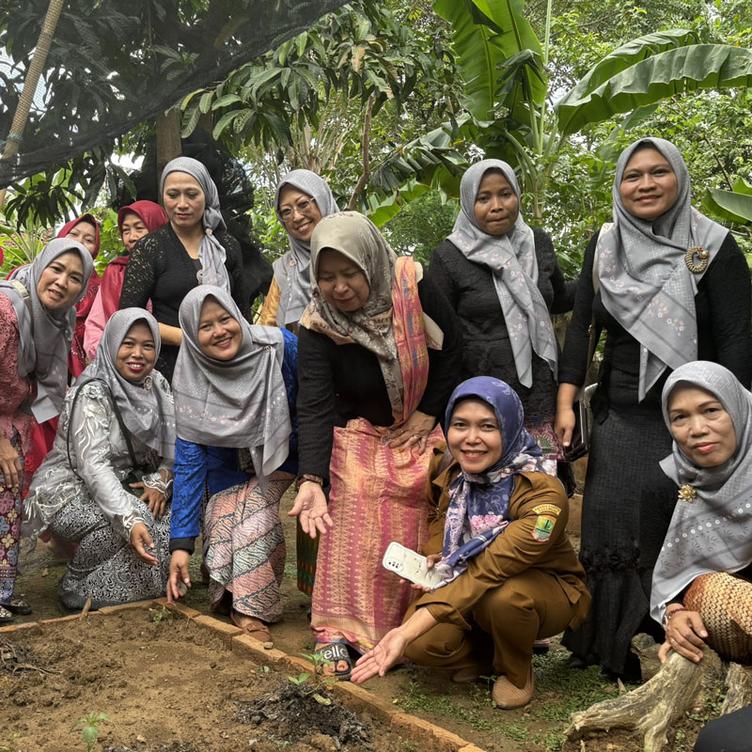
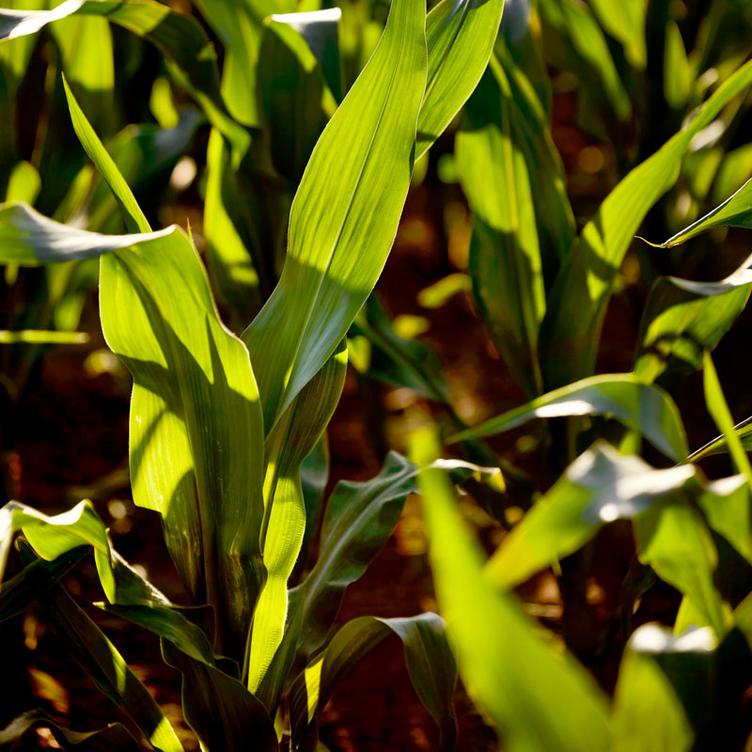
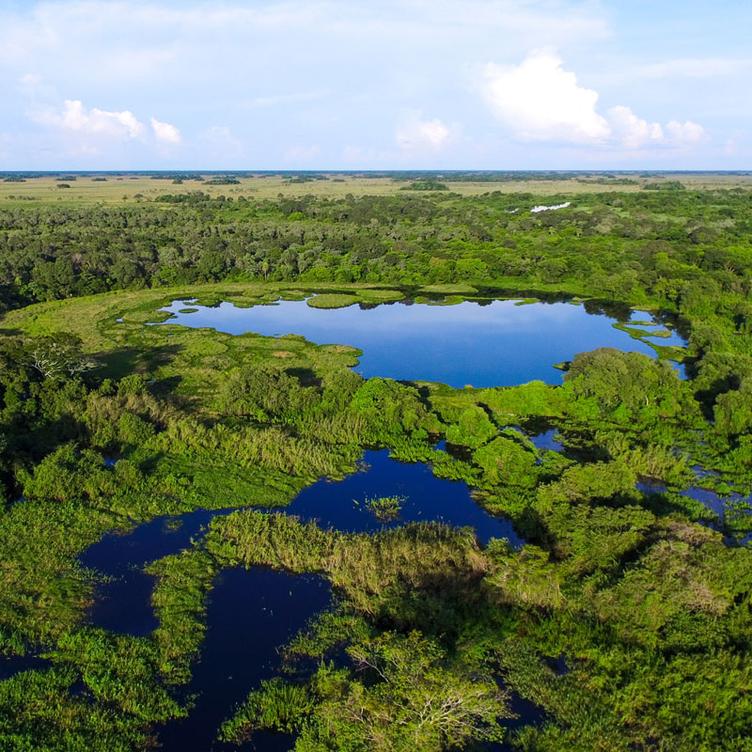
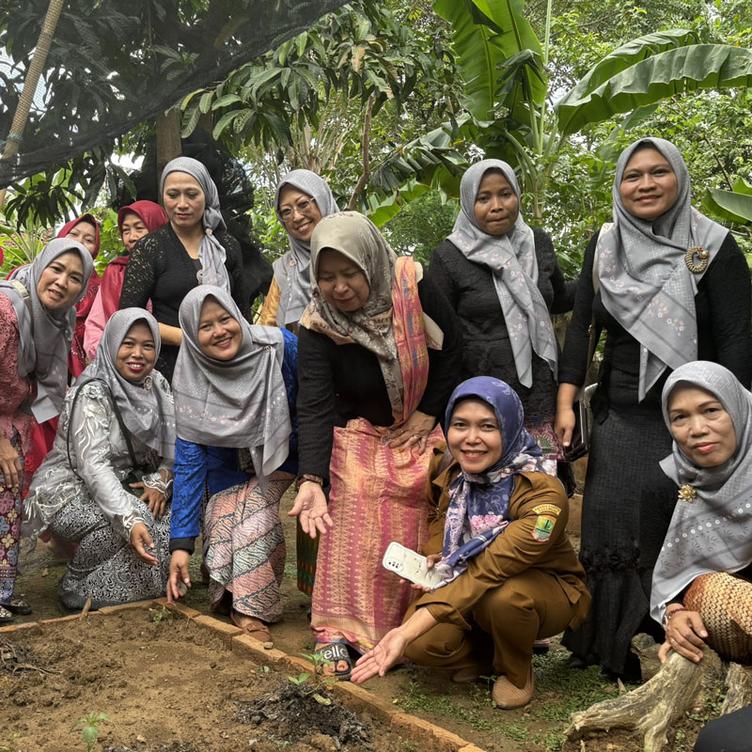
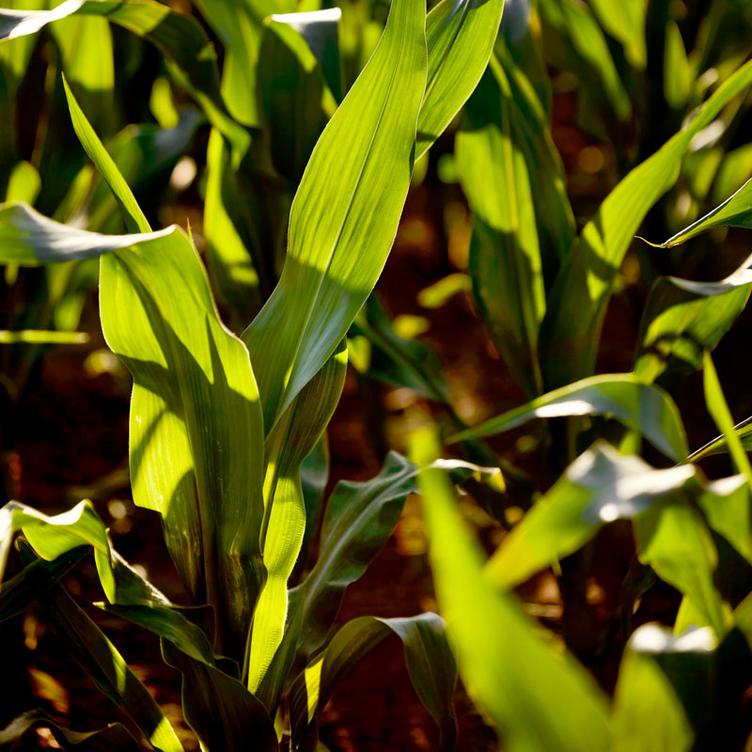
For general inquiries, questions or more information, please reach out to us. We are here to help.
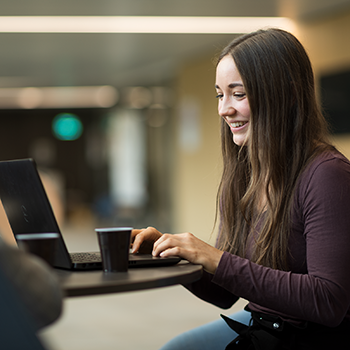
Hi! We're Performing Maintenance.
ERROR CODE: 503
Here are some helpful links
Hello
Need some more information? Complete this contact form and you will be contacted in the next 5 business days.